-
Juan Guevaramuy buen trato con el vendedor y muy buena asesoria y el producto está trabajando muy bien ya tiene un año y no he tenido ningún problema
-
Obert MatetakufaI'm very happy with the business deal and all the support they are giving . A very good business partner
0.75KW Single Phase PLC Servo Drive 16K Step Program Capacity Servo PLC Controller
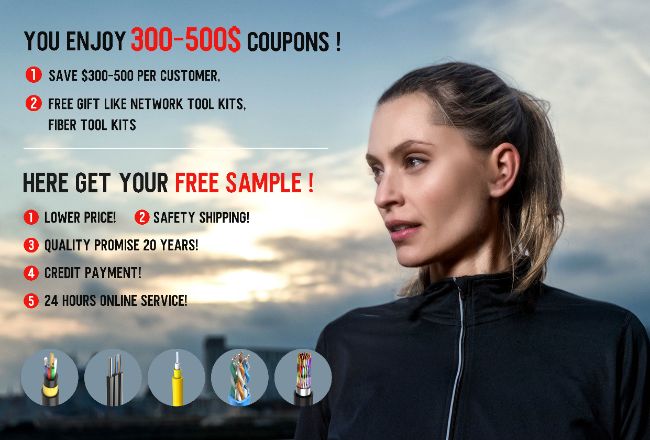
Contact me for free samples and coupons.
Whatsapp:0086 18588475571
Wechat: 0086 18588475571
Skype: sales10@aixton.com
If you have any concern, we provide 24-hour online help.
xVoltage Range | 200V~240V | Circuit Power Supply | Single-phase AC220V |
---|---|---|---|
Rated Power | 0.75KW | Encoder Feedback | 17-bit Single-turn Absolute Encoder |
Program Capacity | 16K/step | Rated Current | 3.0A |
Highlight | 0.75KW PLC Servo Drive,Single Phase PLC Servo Drive,16K Step Servo PLC Controller |
0.75KW Single-Phase Servo Plc All In One Controller 16K Step Program Capacity
Coolmay servo PLC integrated machine is a DSP based, high-performance, high-precision, multi-function, network-based all digital servo driver. Servo PLC integrated machine is also known as "intelligent servo", "programmable servo driver", "programmable servo amplifier", which integrates servo drive technology, PLC technology and motion control technology. Ladder diagram programming can be carried out inside to complete the logic and data operation of PLC, and the synchronous control function of multi axis motor can be realized through the unique motion control instructions.

Technical parameter:
Servo drive series | Mx3g-c40 /C75 series servo PLC all-in-one |
size | 160 * 135 * 42 |
input power |
Main circuit power supply: single-phase AC220V, voltage range 200V~240V, 50/60Hz Control loop power supply: internal conversion, no external power supply |
PLC logic power supply voltage | DC24V |
Drive motor | Linear (DDL), torque (DDR), voice coil, brushless, brushless servo motor |
Control mode | Motion sequence, point to point, electronic gear, position, speed, torque control mode |
Encoder feedback | 17 bit single loop absolute value encoder |
operation mode | Independent programmable control (PLC), external control (step pulse, PWM, encoder A/B), or distributed network control (Modbus/RS communication) |
Communication type | RS485 (supports ModBUS and RS protocols) |
Input,output signal |
16 photoelectric isolated inputs 16 photoelectric isolated outputs, of which three high-speed pulses are programmable and general-purpose |
Rated power (KW) | 0.4KW/ 0.75kW |
Rated current (A) | 2.5A/3.0A |
Rated current range of adaptive motor (A) | 2.0~3.0A/3.0~4.0A |
Program capacity | 16K/step |
High speed processing | I/O refresh command, input interrupt 6 points, timer interrupt 3 points |
Data register | D0~D3999, 4000 points in total |
Operating ambient temperature |
-10~55 ℃ non freezing |
Operating ambient humidity | 10 ~99[RH%] non condensing |
Storage temperature | -20℃~60℃(Maximum temperature guarantee: 80 ℃ for 72 hours) |
Storage humidity | 10 ~99[RH%] non condensing |
Height | Normal use below 1000m altitude, derated use above 1000m altitude |
Vibration / shock | 4.9 (m/s2) /19.6 (m/s2 ) |
Occasion | Indoor, no dust, no corrosive gas, no direct sunlight |
Comprehensive protection design |
Overcurrent, short circuit, grounding, overvoltage, undervoltage, I2t, control error |
Working principle:
DSP (digital signal processor) as the control core, including motion control algorithm, PLC algorithm, servo control algorithm. The power board converts ac to DC through bridge rectifier circuit, and then drives three-phase synchronous AC servo motor through three-phase sinusoidal PWM inverter. The drive board takes DSP as the core and is responsible for signal acquisition, AD conversion, signal monitoring, data processing and data output of each servo module. Through the kernel program for different levels of task scheduling to complete communication, PLC, PWM pulse width modulation, AD conversion, pulse input acquisition and other functions.
Wiring instructions of braking resistor:
If the internal braking resistor is used, the driver should short circuit P and D, that is, it can be used normally according to the factory state, as shown in Figure A. If the external braking resistor is used, the short circuit between P and D must be removed first, and then the external braking resistor must be bridged on P and C, as shown in Figure B: