All Products
-
Juan Guevaramuy buen trato con el vendedor y muy buena asesoria y el producto está trabajando muy bien ya tiene un año y no he tenido ningún problema
-
Obert MatetakufaI'm very happy with the business deal and all the support they are giving . A very good business partner
400W AC Servo Motor 220V IP54 Motor Feedback Level 3000 RPM Rated Speed
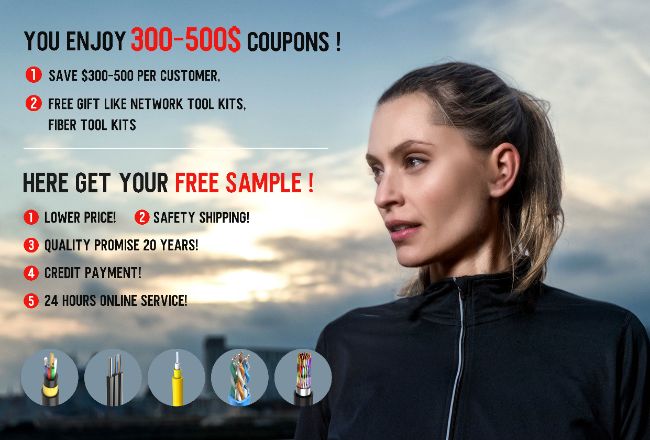
Contact me for free samples and coupons.
Whatsapp:0086 18588475571
Wechat: 0086 18588475571
Skype: sales10@aixton.com
If you have any concern, we provide 24-hour online help.
xProduct Details
Rated Voltage | 220V | Rated Power | 400W |
---|---|---|---|
Rated Torque | 1.27 N.m | Peak Torque | 3.82 N.m |
Rated Current | 2.8±10% AMS | Peak Current | 8.4±10% AMS |
Rated Speed | 3000 RPM | Maximum Speed | 5000 RPM |
Highlight | 3000 RPM AC Servo Motor,AC Servo Motor IP54,Coolmay AC Servo Motor |
Product Description
400W AC Servo Motor 220V IP54 Motor Feedback Level 3000 RPM Rated Speed
Servo motor refers to the engine that controls the operation of mechanical components in the servo system. It is an indirect speed change device of auxiliary motor. The servo motor can control the speed, and the position accuracy is very accurate. It can convert the voltage signal into torque and speed to drive the control object. The rotor speed of the servo motor is controlled by the input signal and can respond quickly. In the automatic control system, it is used as the actuator, and has the characteristics of small electromechanical time constant and high linearity. It can convert the received electrical signal into the angular displacement or angular speed output on the motor shaft. Its main feature is that when the signal voltage is zero, there is no rotation phenomenon, and the speed decreases uniformly with the increase of torque.
Parameter:
Installation notes
1. When the installation/removal part is at the end of the motor shaft, please do not knock
the shaft hard to prevent the encoder at the other end of the shaft from being damaged.
2. Try to prevent the shaft seat from vibrating to prevent damage to the bearing.
Recommended Products